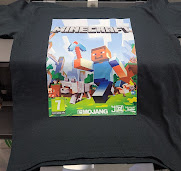
Thursday, July 15, 2024
Let's Talk About Temp, Time and Pressure. How To Heat Apply DTF.
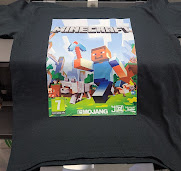
Thursday, July 1, 2024
DTF vs. HTV Which is right for you?
If you are an avid crafter or a shirt decorator, you have probably stumbled across a post or video about DTF printing.
What is DTF printing? DTGPro explains it like this..."DTF is also referred to as Direct Transfer Film, and it works by printing transfers that are heat pressed to a variety of garments (and other substrates). There are many compatible fabrics including cotton, nylon, leather, polyester, and 50/50 blends. This is unlike DTG technology which only works on cotton fabrics. This therefore means that this printer works on a much wider substrate, making it the most versatile digital printer in the market. DTF printers work on both white and dark garments and can get the job done without requiring you to press on costly A+B paper, as is the case with the white toner printers.
Direct Transfer Film printers also combine reliability, unmatched quality and high productivity. They can handle large production volumes, which is essential in this fast-growing industry. Unlike DTG technology, DTF printers are preferred by most people because they are affordable and require no pre-treatment. For quality results, you will need DTF powder and DTF sheets to print transfer film, and of course, DTF Ink.
Another advantage of DTF printing over traditional printing is that it is highly sustainable. There is no question that the fashion industry is increasingly focusing on sustainability."
- Printer that has been or can be converted for DTF printing. (list of printers)
- Rip software for printing. (for more info, google rip software)
- DTF Ink
- Refillable ink cartridges and syringes
- PET film to print on
- Adhesive powder
- Heat source to cure adhesive powder
- Heatpress to press finished transfer onto garment.
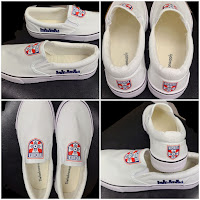
Wednesday, October 4, 2017
October Update!
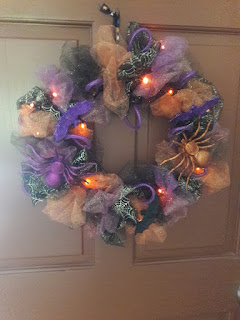
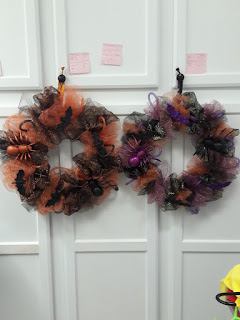
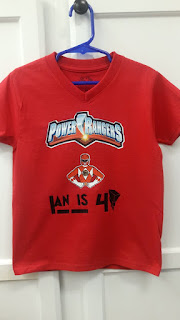
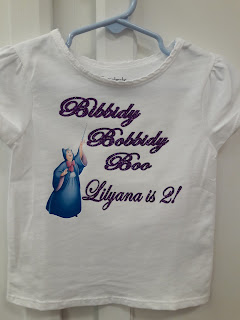
In the mean time my massive paper collection is sitting idle wondering when I will start using it again, while my heat transfer vinyl collection is growing. But I have my papers picked for the coach and I'll be cutting and gluing it this weekend.
Thanks for stopping by!
Wednesday, April 26, 2017
Crazy about HTV!
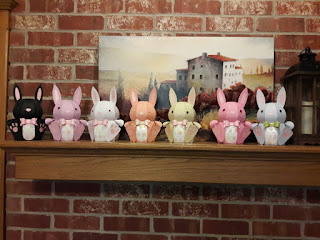
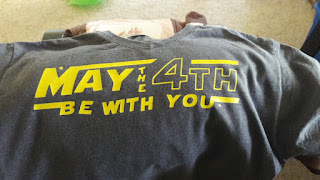
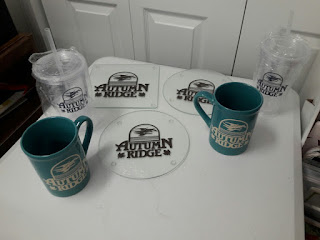
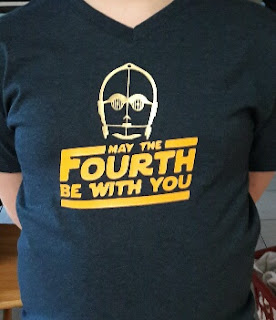
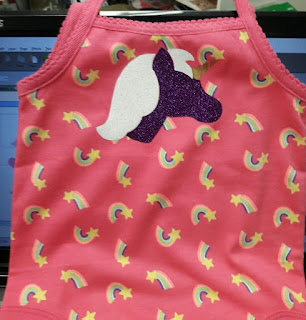
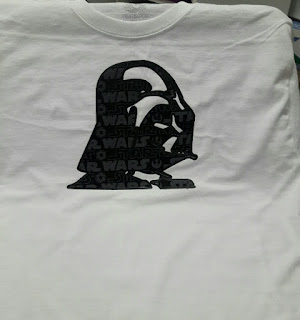
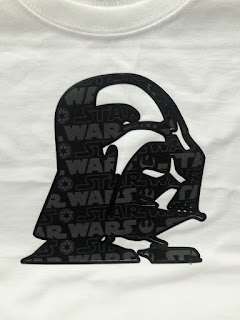
Have You Been Missing Out?
Below are the fun giveaways that have be going out the last few weeks. Only 2 more Wednesdays until Christmas! That means only 2 more give...
-
With every new thing, comes new challenges. DTF is my new thing. Finding information on how to heat apply was a toss-up for awhile. Here ...
-
If you are an avid crafter or a shirt decorator, you have probably stumbled across a post or video about DTF printing. What is DTF printing...
-
I was shopping at one of my area Dollar Trees the other day and saw a shelf full of Crafter's Square vinyl! So, I bought one of each co...